how to add carbon to steel
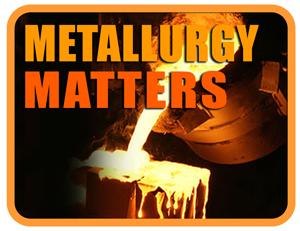
Generally, carbon is the most important commercial steel alloy. Increasing carbon content increases hardness and strength and improves hardenability. But carbon also increases brittleness and reduces weldability because of its tendency to form martensite. This means carbon content can be both a blessing and a curse when it comes to commercial steel.
And while there are steels that have up to 2 percent carbon content, they are the exception. Most steel contains less than 0.35 percent carbon. To put this in perspective, keep in mind that's 35/100 of 1 percent.
Now, any steel in the 0.35 to 1.86 percent carbon content range can be hardened using a heat-quench-temper cycle. Most commercial steels are classified into one of three groups:
- Plain carbon steels
- Low-alloy steels
- High-alloy steels
Plain Carbon Steels
These steels usually are iron with less than 1 percent carbon, plus small amounts of manganese, phosphorus, sulfur, and silicon. The weldability and other characteristics of these steels are primarily a product of carbon content, although the alloying and residual elements do have a minor influence.
Plain carbon steels are further subdivided into four groups:
- Low
- Medium
- High
- Very high
Low. Often called mild steels, low-carbon steels have less than 0.30 percent carbon and are the most commonly used grades. They machine and weld nicely and are more ductile than higher-carbon steels.
Medium. Medium-carbon steels have from 0.30 to 0.45 percent carbon. Increased carbon means increased hardness and tensile strength, decreased ductility, and more difficult machining.
High. With 0.45 to 0.75 percent carbon, these steels can be challenging to weld. Preheating, postheating (to control cooling rate), and sometimes even heating during welding become necessary to produce acceptable welds and to control the mechanical properties of the steel after welding.
Very High. With up to 1.50 percent carbon content, very high-carbon steels are used for hard steel products such as metal cutting tools and truck springs. Like high-carbon steels, they require heat treating before, during, and after welding to maintain their mechanical properties.
Low-alloy Steels
When these steels are designed for welded applications, their carbon content is usually below 0.25 percent and often below 0.15 percent. Typical alloys include nickel, chromium, molybdenum, manganese, and silicon, which add strength at room temperatures and increase low-temperature notch toughness.
These alloys can, in the right combination, improve corrosion resistance and influence the steel's response to heat treatment. But the alloys added can also negatively influence crack susceptibility, so it's a good idea to use low-hydrogen welding processes with them. Preheating might also prove necessary. This can be determined by using the carbon equivalent formula, which we'll cover in a later issue.
High-alloy Steels
For the most part, we're talking about stainless steel here, the most important commercial high-alloy steel. Stainless steels are at least 12 percent chromium and many have high nickel contents. The three basic types of stainless are:
- Austenitic
- Ferritic
- Martensitic
Martensitic stainless steels make up the cutlery grades. They have the least amount of chromium, offer high hardenability, and require both pre- and postheating when welding to prevent cracking in the heat-affected zone (HAZ).
Ferritic stainless steels have 12 to 27 percent chromium with small amounts of austenite-forming alloys.
Austenitic stainless steels offer excellent weldability, but austenite isn't stable at room temperature. Consequently, specific alloys must be added to stabilize austenite. The most important austenite stabilizer is nickel, and others include carbon, manganese, and nitrogen.
Special properties, including corrosion resistance, oxidation resistance, and strength at high temperatures, can be incorporated into austenitic stainless steels by adding certain alloys like chromium, nickel, molybdenum, nitrogen, titanium, and columbium. And while carbon can add strength at high temperatures, it can also reduce corrosion resistance by forming a compound with chromium. It's important to note that austenitic alloys can't be hardened by heat treatment. That means they don't harden in the welding HAZ.
|
* Stainless steels always have a high chromium content, often considerable amounts of nickel, and sometimes contain molybdenum and other elements. Stainless steels are identified by a three-digit number beginning with 2, 3, 4, or 5. Figure 1 |
Steel Classification Systems
Before we look at a couple of common steel classification systems, let's consider one more high-carbon metal, cast iron. The carbon content of cast iron is 2.1 percent or more. There are four basic types of cast iron:
- Gray cast iron , which is relatively soft. It's easily machined and welded, and you'll find it used for engine cylinder blocks, pipe, and machine tool structures.
- White cast iron, which is hard, brittle, and not weldable. It has a compressive strength of more than 200,000 pounds per square inch (PSI), and when it's annealed, it becomes malleable cast iron.
- Malleable cast iron, which is annealed white cast iron. It can be welded, machined, is ductile, and offers good strength and shock resistance.
- Ductile cast iron, which is sometimes called nodular or spheroidal graphite cast iron. It gets this name because its carbon is in the shape of small spheres, not flakes. This makes it both ductile and malleable. It's also weldable.
Now let's take a look at a typical steel classification system (see Figure 1 ). Both the Society of Automotive Engineers (SAE) and the American Iron and Steel Institute (AISI) use virtually identical systems. Both are based on a four-digit system with the first number usually indicating the basic type of steel and the first two numbers together indicating the series within the basic alloy group.
Keep in mind there may be a number of series within a basic alloy group, depending on the amount of the principal alloying elements. The last two or three numbers refer to the approximate permissible range of carbon content in points (hundredths of a percent).
These classification systems can become fairly complex, and Figure 1 is just a basic representation. Be sure to reference the most recent AISI and SAE publications for the latest revisions.
That's a look at some basics concerning the iron-carbon-steel relationship and its influences on welding and metal alloys. Next time we'll look at hardening and ways to make metals stronger. We'll also consider the influences of some key alloying elements and the effects of welding on metallurgy.
You May Also Like
how to add carbon to steel
Source: https://www.thefabricator.com/thewelder/article/metalsmaterials/carbon-content-steel-classifications-and-alloy-steels
Posted by: plantlicedle.blogspot.com
0 Response to "how to add carbon to steel"
Post a Comment